Everybody looks for speed at work, which translates into process efficiency. But what does speed mean? A quick press brake is not that which axels Y, X, R and possibly Z are quicker than the others.
The speed of a press brake is compared only to the quality it offers to the whole production process.
For this, it is important to know the evolution of technology and the limits that have been gradually overcome: this is useful to choose the quickest machine according to what we produce and what is offered by the market.
Speed is, therefore, a partial component that can be reached only along with an evolved press brakes' builder and can be overcome thanks to most suitable suggestions for your needs.
But first of all, it is necessary to know more about the obsolete technologies that in the past contributed to reach the current standards.
If the "three-points" bending (see bending manual) is about a relatively simple notion, during the years many technologies have tried to get the same effect, that is the controlled approach of a stamp to a mold in the most precise and quick way.
Mechanical press brakes
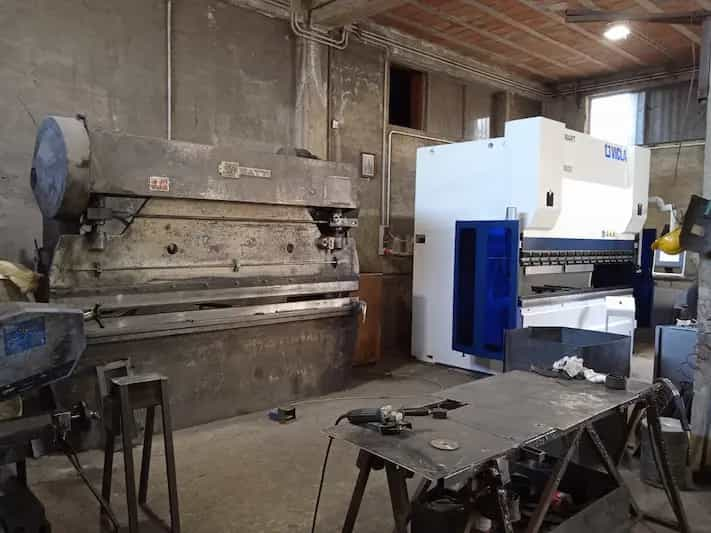
It was the first bending press, now it is obsolete. Connected to a flywheel and with a movement similar to the one given by molding eccentric presses, they gave a focused and apparently rapid push.
Indeed, with no precision nor adjustable gauges, the speed of axel Y is not enough to really improve the process.
Moreover, they were really dangerous.
RG Promecam
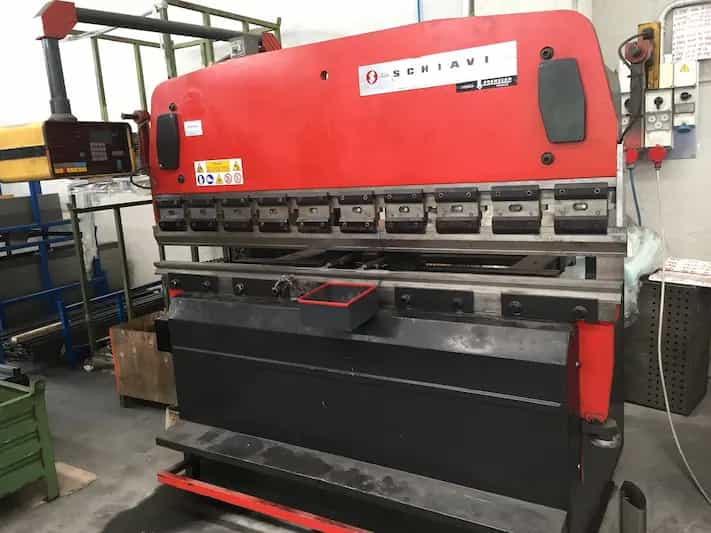
One of the most historical machines, produced by the French company Promecam that doesn't exist anymore. Unconventionally, it worked the other way around (it went upside to fix stampings, rather that downside).
Torsion Bar Hydraulic Press Brakes
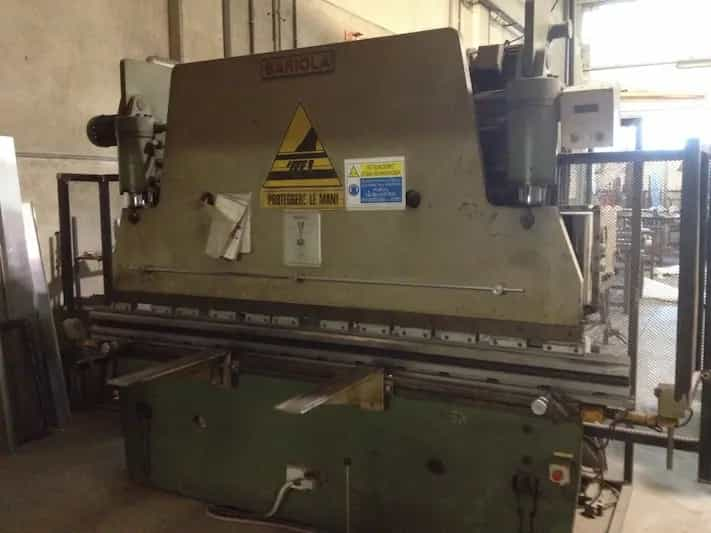
Apparently identical to synchronized hydraulic press brake still used today, they represent their forerunner. The descent of the two cylinders was synchronized by a system of levers connected to a torsion bar.
The limits, instead, were often made by two pieces moved by universal joints that shifted the cylinders setbacks.
Synchronized hydraulic press brakes
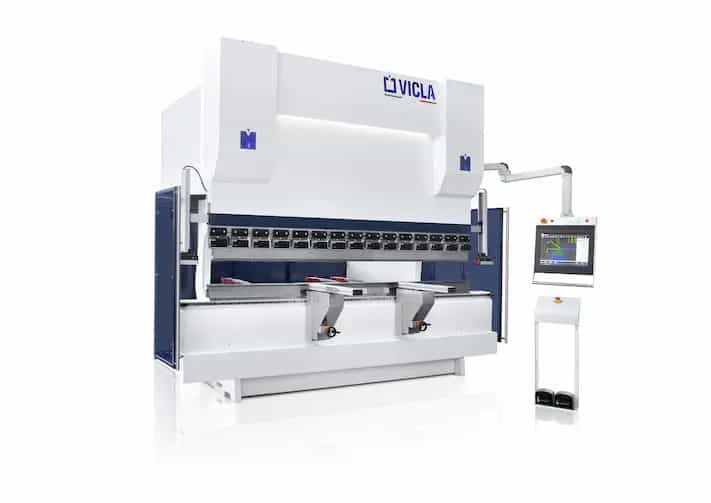
They represent the majority of the machine used today.
The two cylinders are independent and moved by the action of dedicated valves.
They are a great compromise to reach the speed needed.
Also, the technology used is established and reliable: since various tools can be added (multi-axels back gauges, graphic numerical controls and many more), it may represent the most suitable technology for you.
Hybrid hydraulic press brakes

Sometimes called electrical press brakes, they are the natural evolution of synchronized hydraulic machines. In this case there is a very high speed, thanks to the match between a great precision and the technologies just described. The secret is the presence of two brushless engines that directly move two separate small oil tanks. It follows that speed and precision go hand in hand with reduced consumptions.
Electrical press brakes
They represent a niche because they are suitable only for specific works.
They can be moved by belts or by recirculation screws in traction or in pressure.
Another aspect, that may not seem to be connected with speed, is its dimension: this is especially important if thinking in terms of workflow speed and not relying on a single machine. This could be the case of who produces the 80% of pieces or more which bending is under 1500-2000 mm. A valid alternative can be relying on a builder that has on the catalogue a very small and speed machine that does most of the work in terms of variety and tools.
