Let’s further discuss the fundamental aspects that need to be analysed before choosing a press brake. Due to the complex nature of the machinery, it is often difficult to precisely pinpoint the elements that can guarantee reliability, robustness, safety, predictability of processing over time, complexity of the achievable bends...
Many of these elements are substantially hidden, and this is the most important decision risk factor, because it is precisely on these details that the soundness of the investment is based.
So what are the key elements to examine before signing a contract for press brake supply?
#1: the Structure
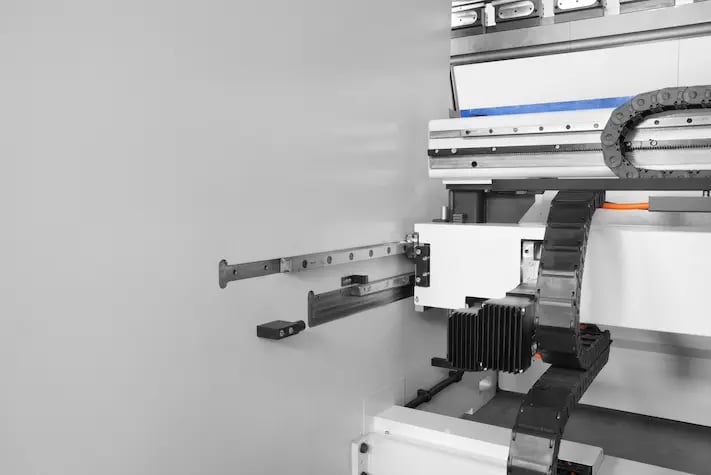
The frames are the part of the machine that is assigned to withstand stresses when the bending action is carried out: a weak structure will tend to deform, compromising the quality of the end product.
Research carried out over the years on bending of the structure have allowed us to design and build a press brake that appropriately responds to mechanical stress. The frames are cut after rolling the plate: this apparently secondary measure ensures that deformation evenly takes place on both sides, with the benefit of obtaining bends with consistent angles.
The parallelism of the frames is guaranteed by processing with centesimal tolerances and allows greater accuracy, repeatability and speed of the back gauge to be obtained. This technical-structural peculiarity eliminates vibrations and stresses, allowing the gauge to move at high speeds, without neglecting positioning accuracy.
#2: the Double Guide
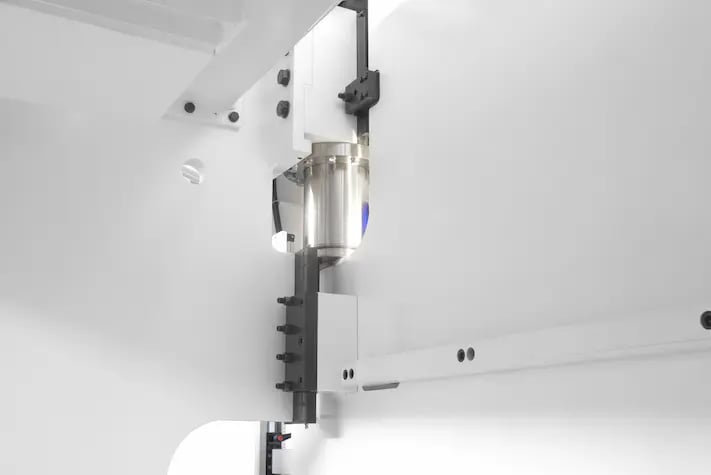
The guides have the function of maintaining the stability and the perpendicularity of the upper beam with respect to the work surface. This allows bending precision to be maintained with different tools and intermediaries, ensuring centrings is maintained over time as carried out on testing.
This is a particularly important detail, because in the absence of this measure, the operating time of the press translates into a progressive loss of perpendicularity, initially inadvertent but gradually more invalidating of the centrings, until it has to be serviced.
#3: the Cylinders
Cylinders are a fundamental component of a press brake. They can be made from a tubular or rectangular part.
VICLA chose to make them starting with a block of forged C-45 material. The upper part of the sleeve has a removable hydraulic block mounted to facilitate routine maintenance operations; the shafts are tempered and ground. The cylinders are connected to the upper cross beam by means of a semi-sphere that allows you to carry out any type of processing, even the most particular such as those requiring different angles between right and left.
#4: the Hybrid System
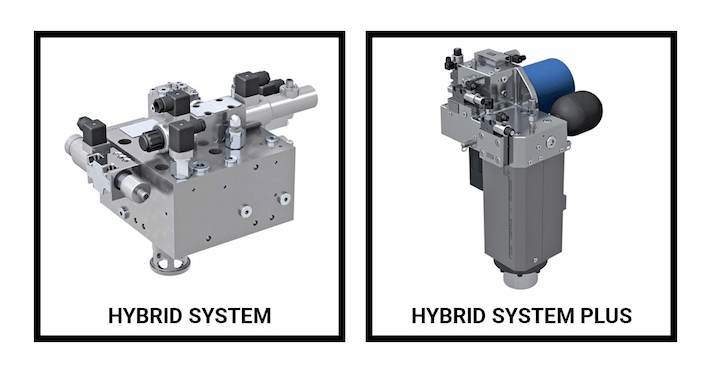
If in the past there were few types of bending machines, nowadays the market offers different choices:
- hydraulic press brakes;
- electrical press brakes;
- hybrid press brakes.
These machines differ from one another in technology and construction methodology. In VICLA, we have always believed in the potential of hybrid technology. To ensure optimal performance by increasing productivity without compromising consumption, our choice was to design press brakes equipped with an innovative hybrid system.
Be careful, though! It is not enough to just add an inverter to call a press brake "hybrid"; in fact, technological innovation revolves around a specific hydraulic system, which in the case of the standard hybrid model, includes a completely independent dual hydraulic circuit, each equipped with its own tank, motor, pump and inverter.
The functional separation of the two cylinders allows optimised control according to the load required for each cylinder; moreover, it allows efficiency to be achieved in terms of energy.
It is a system able to minimise wear of the machine by concentrating all its efficiency and automatically balancing the working pressure exclusively on the side that is used during bending of that specific part.
A further level of performance is provided by the Hybrid Plus model: the system consists of a brushless motor for each cylinder, capable of providing high forces and high movement speeds. It is an even more compact system consisting of a direct drive motor and pump, installed directly on the cylinders. with significantly reduced piping.
It is not wrong to say that the hybrid model is an evolution of the hydraulic press brake. In fact, it is an enhanced and improved bending machine thanks to the latest generation of electro-hydraulic components: This hybrid bending machine combines the best of electric presses and hydraulic bending machines.
The results in numbers of this technological innovation are significant, as seen on the graph.
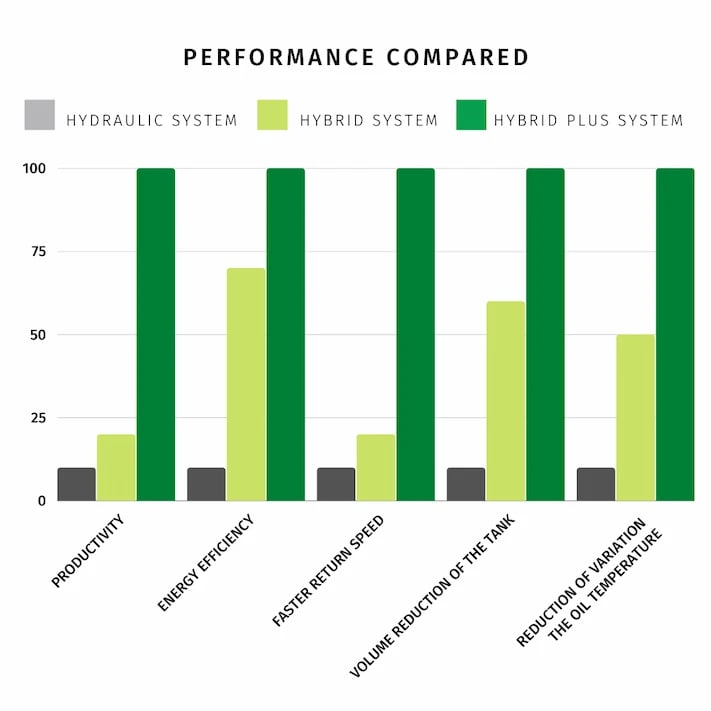
#5: the Clever Crowning
The greater the length of a bending machine, the more the problems relating to the structural failure of the bench, making it more difficult to get a well-processed part. Over the years, technological evolution has taken giant steps, passing from manual systems (such as using paper shims under the matrix) to automatic, mechanical or hydraulic systems, where a pre-load of the assumed deformation was determined. The limit of these systems is based on a theoretical calculation set by numerical control.
VICLA has developed an intelligent system that improves the work in the workshop: the active Clever Crowning system.
The active crowning system automatically calculates the thrust force of the bench cylinders, based on the specific sensors detected on the upper and lower beam. By doing so, the necessary corrections are calculated in real time for each bend made, obtaining linear bending over the entire length.
What are the advantages of this "intelligent" system? Mainly three:
- it ensures great results even in the presence of an inexperienced operator;
- it uniforms the bending angle without any need for operator intervention;
- it guarantees a perfectly linear bend even on uneven materials (e.g. perforated/slotted mixed with solid material).
#6: the Flex
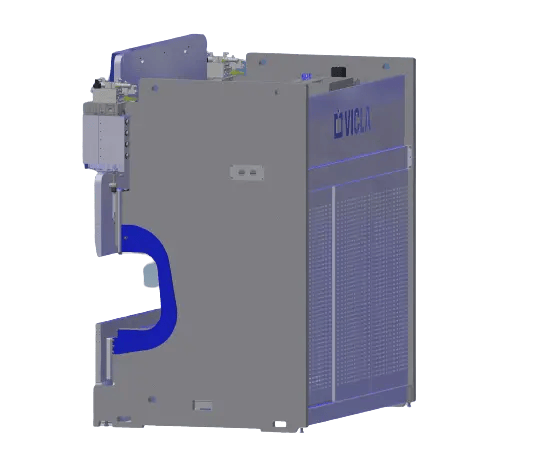
Flex is the innovative control device of structural bending of frames to maintain the same depth of bending regardless of the length of the metal sheet.
Each press brake, however robust, undergoes structural flection during the bending phase, and obviously the deformations are greater the more force the machine must use.
The main deformation is crowning, which corresponds to bending the beam that is pushed into position by the side cylinders; the other (and in many ways semi-unknown), is what is called in Italian jargon "yawn" and it is the tendency of the frames to open in the recess area.
Thanks to the Flex system, the machine dynamically compensates for any deformation according to the effort required: the CNC receives data from the cylinder pressure sensors, which are interpolated in real time in order to establish the correction to carry out.
#7: the Back
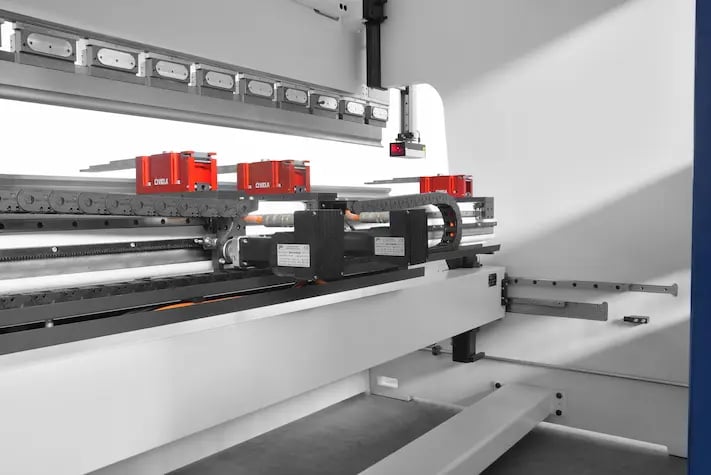
The rear references are another hidden yet very important element. In VICLA, we have chosen to install references with particular structural technical peculiarities:
- Mechanics mounted directly on the frames machined with centesimal tolerances and equipped with brushless motors with integrated electronics managed in CANopen for high performance;
- Transmission on ground racks that guarantee high axis speed (560 mm/s) and positioning accuracy (+/- 0.02 mm): this allows high production cycles, high quality standards, high precision and silence;
- New gauge composed of a 10 mm structural beam thickness with an innovative parallel adjustment system for maximum flexibility of composition and customisation and extreme rigidity and strength;
- Sliding towers on 2 opposing linear guides adjustable from the front of the machine with pneumatic release. The basic BACK has 2 axes (X, R). It is also possible here to make a further upgrade up to a maximum of 6 axes (X, R, Z1, Z2, X2, X3). All towers are equipped with a LED visual stop. Lighting of the LED ensures contact of the sheet with the reference.
Ultimately
We analysed the main hidden elements to focus on in the selection of a press brake, to ensure that it is a profitable investment over time, capable of:
- reducing operating costs;
- maximising productivity;
- achieving the most in terms of processing quality.
By doing so, even the end client can count on a standardised and reliable supply.
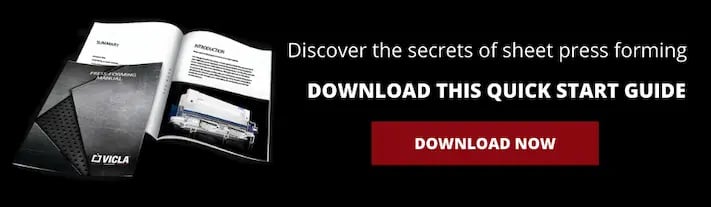