The beam lowers, first aligned, then it goes down on one side.
At the same time, a yellowish trickle pours down from the crankcase of one of the two cylinders.
The situation is clear: the press brake is broken.
The moment in which the damage occurs, you start counting your losses, an activity that bears the name of calculation of lost earnings from lost profit.
It is difficult to quantify the waste of money, only after careful analysis is it possible to have a plausible estimate of its extent.
It must be said that, unfortunately, collecting data costs time and effort.
However, if we do not rely on precise and reliable numbers, we will not have an indication of which ones are the really convenient choices for our company.
This is why it is very important to catalog the costs of a machine downtime.
Some are intangible and difficult to estimate, but most are absolutely recognisable in a short time, by answering a few simple questions:
1) How much does your press brake operator cost?
A bender is usually a skilled worker, so he is not the one with the lowest salary as he creates some type of added value.
From the moment this element goes missing, the cost for the company immediately begins to have a certain weight.
He could, perhaps, devote himself temporarily to other tasks, but the bending department will certainly travel at reduced speed due to machine downtime.
2) How much does the assistance cost?
It depends on whether an agreement has been made with the manufacturer.
Often, if the machine is not new, you can turn to the parent company service or to freelance technicians.
In any case, there is an hourly cost to be incurred, which obviously increases in relation to the duration of the repair.
3) How much do the spare parts of our press brake cost?
And let's add, how easy is it to find them?
Their cost is what we immediately see, but the difficulty in finding them immediately extends the downtime, increasing the cost of the first point, and all the others that we will see later.
Among the costs that cannot be quantified quickly, but that can have heavy implications, there are what we could define as "risks", including:
-
-
Stress of the adjacent units
In other words, it means that the work that the faulty press brake does not do must be disposed of by the other machine(s) present in the company.
Often this leads to an acceleration of processes which can increase the chance of error.
Or, the need to increase the hours of employees, or add a shift for the entire downtime.
All this has an obvious impact on the total cost of the breakdown.
-
Manufacturing outsourcing.
Contacting a workshop that carries out our same business could be a solution to temporarily solve the problem of halted deliveries.
Obviously the cost of labor will be different, and is added to all other costs determined by the machine downtime.
-
Delivery delays.
This is the worst risk that a subcontractor can face, together with the non-conformity of the processed parts.
Unfortunately, the consequences of this disservice can be different and depend on the type of relationship with your customers. With some, a late delivery can result in a penalty, which partially or totally affects your earnings. With others it can lead to the end of the business relationship, especially when it has just begun.
So, you should always ask yourself "how much does a downtime cost?" whenever you’re choosing the supplier and the press to buy. It is necessary to look beyond appearances to see beyond the price!
Choosing your next press is therefore a crucial choice that will determine your production. Choose the one that suits you best: trust the experts!
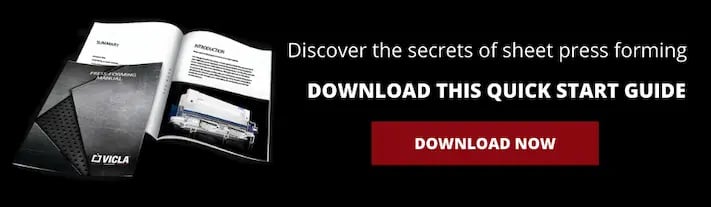