Nowadays it’s possible to have both speed and accuracy when bending sheet metal, you just have to know how to choose: in fact, to create this apparently impossible marriage, you need a press brake that provides real added value to the production chain.
Today we will find out what are the most important – and often overlooked – things to consider to finally have speed and accuracy in your company at the same time.
Sheet meal bending brings with it physiological issues, first of all from a number of environmental and material variability factors.
The production line of a sheet metal workpiece is similar to a chain, which begins with an idea developed in a technical office, which is subsequently roughed during the cutting phase, to then be “brought to life” and given form by the press brake.
If every link in the chain is not high quality and well lubricated, your company's movement risks jamming or working badly, resulting in unacceptable speed and efficiency losses.
That is why it’s counter-productive to invest inconsistently in the technologies you need.
For example: it’s unreasonable to think of reducing waste sufficiently by purchasing a laser cutting machine of the latest generation, a champion of speed, if you then accompany it with an obsolete or low-cost press brake.
So here are some tips to avoid having to choose between speed and accuracy.
1) Choose a robust, well-built machine
Being able to count on machines designed specifically and manufactured with care and quality is a key factor in ensuring speed and accuracy at the same time.
In this sense, made in Italy is in itself a great business card, especially considering experience, professionalism, capability and general quality.
Contrary to any false stereotypes, Italy is one of the top five countries in machine tool production, and it’s no coincidence that the sector worldwide has always recognized Italian manufacturing as offering great added value.
2) Choose a manufacturer that listens to you
This is a much undervalued issue, but several sources confirm that choosing a good machine without having the same good support can turn out to be completely counter-productive.
For example, relying on a manufacturer that is smaller in size but large in service gives a huge competitive advantage that is hard to quantify.
What you need is a partner that is willing to let you visit its site, talk to its owners and employees and, of course, directly to its service department for any need. Because speed and accuracy must also go together in support.
3) Choose a manufacturer that focuses on your needs
If you need a particular component or accessory in order to work with speed and accuracy, it's good if the manufacturer has it in its catalogue and, above all, that it can advise which one is best for you with transparency and expertise.
Sheet metal bending supports, hybrid technology, multi-axis backguages, quick tool connections, etc.
All devices that should never be considered a running cost, but a real investment to improve process quality and effectiveness.
Therefore, bending speed and accuracy can only coexist if you have a high-quality machine made by a professional manufacturer that is willing to listen to your needs. These have become essential conditions in order to ensure that your work provides added value.
None of your customers will ever be willing to pay a premium for waste because your machine is slow and inaccurate, especially in an extremely competitive market like ours.
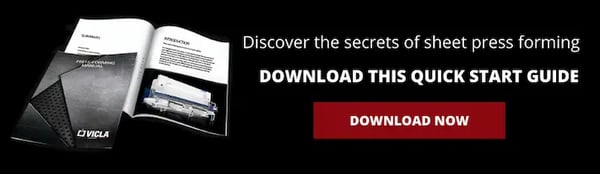