There are several laws and safety certificates to be considered both in Europe and outside, because press brakes are a type of machine that involve many laws according to the safety disposal used on the machine itself. Let’s try to understand the importance and the application fields of such laws, but also legislative decrees of who is subjected to suc obligations and how this can help to choose the best in the field of press brakes.
The importance of certifications
Products manufacturer are the first to be involved in the field of laws and certifications: once identified the press brake, it is important trying to understand if it respects the standards required by rules or laws. In this regard, we consulted the Inail manual (ex Ispesl) for the safe use of press brakes (Caratteristiche di funzionalità e sicurezza dei dispositivi a protezione del fronte lavorativo delle presse piegatrici idrauliche, Features of functionality and safety of devices to protect the working front of hydraulic press brakes). Legislation is made of already operating State laws (in this case we refer to "Presidential Decree of April 27th 1955 n. 547 "Norme per la prevenzione degli infortuni sul lavoro", Rules for the prevention of accidents at work), as well as European directives that became laws and apply to machines where there is a significant number of cold working of metals machines.
Regulations, laws and decrees in Italy
The contents of the said Decree are applied to residential Decree 547/55 to press brakes, more in general to Title IV "Norme particolari di protezione per determinate macchine" (Special protection rules for specific machines) in chapter VI "Presse e Cesoie" (Presses and shears):
- 115 says that presses, shears and similar machines must be equipped with shelters or disposals in order to avoid that hands or other parts of the body are hurt by the stamp or by other mobile working organs;
- according to 117 a slow movement or other similar disposals or expedients to avoid possible dangers must exist;
- 78 involves the presence of a foot control;
- 77 involves set in motion controls;
- according to 76 every machine must have easy-to-recognize and clearly to access start and stop controls.
Safety requirements
Therefore, the manufacturer must produce machines that respond to essential safety requirements, but we highlight that the document of a technical rule is mandatory only if it is required by a law, otherwise the manufacturer can insert such rule only on a voluntary basis. Later we will see what are the systems and technologies for which Italy and the European Union get busy.
Systems: pros and cons
Different systems, different pros and cons. What we have just said about rules and decrees actually reverses on technology: as regards the photo-electric barrier, the limitations of use are those of pieces and boxed of small dimensions, the reflection possibility of infrared rays while using mirroring metal sheets or the danger for the operator if s/he fails to set the muting point; while the pros are the high performances, the possibility to operate with barrier both vertically and horizontally and with every type of tool. The advantage of laser systems that moves with the crossbeam is the possibility to work with little pieces and boxed, and the limitation of use regards a higher muting point and the respect of the safety distance only in particular working condition; the danger is in case of stamp replacement.
Old inadequate technologies
For the monitoring systems fixed to the press brake board there is laser monitoring that, like inconsistent light monitoring (we will see it later), is no longer representative of the state-of-the-art of these machines. The first one doesn’t ensure a complete protection of the dangerous area, it is obliged to frequent adjustments of the laser beam and, in case of uneven metal sheets, the adjustment is difficult to achieve. Instead, the infrared ray of the inconsistent light monitoring can be reflected by the metal sheet in progress and the ray divergence doesn’t ensure the proper Tx-Rx operation.
Now we will try to understand the different features it must have to be considered safe by law.
The importance of the various stages
“During the design stage, the press brake already has to take into account the security integration principle that concerns not only the use of the press on duty, but also the regulation, maintenance, assembly and dismantling stages” the Inail Security Manual on press brakes quotes. So, the best moment to achieve the goals and secure press brakes is – as can be deduced – during the design stage, because during the metal sheet pressing nothing can be left to chance and to reach such goals we start from the premise that the mchine we want to buy and use must be safer than a spaceship.
Factors to be considered
Let’s start from this: muting and blanking.
Muting is about the fact that press brakes are usually designed so that for a stretch of race, the stamp has a certain speed (e.g. 100 mm/s). Later, at a point called “muting” programmed when the CNC is on board, the stamp continues its race at low speed until it performs the fold (≤10 mm/s). This is possible only if the machine has a hold-to-run device and a system with a photocell system device.
Blanking, instead, is a feature available for optical barriers: in some parts of the sensitive field they can be disabled. This means that one or more areas of the detection area of the optical barrier are made inactive to allow a part of the performing piece to enter a detection area without activating the protective device. Suppression can be incorporated into the optoelectronic protective device only as long as the safety distance is such as to guarantee that reaching the dangerous area is impossible.
Other security points
We know that a single post can’t explain all the topic, so here it is an hypothetical list to consider when buying a good press brake: for example, we need to consider the setting of the physical barriers (guards that can be of two types: fixed, at total segregation, that avoid the access to the dangerous area on all sides, solidly fixed to the machine, to another rigid structure or to the ground; and the one called “interlocked guard” associated to a micro-switch made for avoiding the access to the dangerous area during any dangerous movement, if used along with fixed guards) and intangible barriers (that is, safety photocells made of electro-sensitive protection devices that use opto-electronic protection devices active where the operator safety is given by the detection of that part of the human body that enters the dangerous zone and provokes the stop of dangerous movements).
And then, in vertical or horizontal position, laser scanner systems, two-hand control, with other body areas to be protected, such as the front, side and back areas of who works with a press brake are just some of the factors to consider when talking about safety of machinery.
Designers, manufacturers and safety
Designers have to take all the practical measures to ensure that the devices inserted into the designing machines don’t become a danger for whoever assemble, install, keep or make fixings, while the designers, manufacturers and suppliers of press brakes and individual protection devices have legal duties that must satisfy also all the international laws.
Indeed, the different control system such as the two-hand one and the three-position pedal and, more in general, all the press brake control systems and the associated safety components (laser, scanner, and so on) have a primary relevance for press brakes.
Considering all the features just listed, a greater security will be achieved, even when buying a used product: wide and well stocked and, as we noticed, that every manufacturer has in the company.
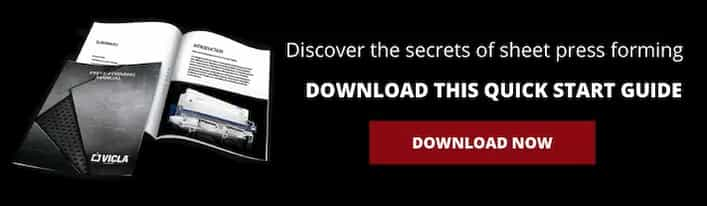
