A press built to the highest standards, with numerous process parameter checks and alarms to warn when any of them drifts is able to maintain a consistent level of bend quality, but there is much more to be considered.
The spring back variable
Let’s look at sheet metal bending: it’s a material with many variables: bending response to laser cutting, plasma cutting, size tolerances and so on. Whenever you have to tackle a different workpiece, you also have to think about aesthetics if you are dealing with materials such as pre-painted sheets and steel. For those working with the press brake, everything has to do with the ever-present forming variable: spring back.
This is a variable that occurs when the material attempts to return angularly to its original shape after being bent. Tensile strength, material thickness, tool and press brake type naturally all affect spring back. It is essential to predict and evaluate spring back effectively, especially when working with tight bends, as well as with thick, high-strength materials.
Laying out workpieces for bending
The material normally deforms during bending. The length of the workpiece to be bent is naturally not the same as that of the axis of the bent workpiece. The axis that retains its original line (known as the neutral axis) shifts towards the inside of the bend, and its position depends on various factors such as the sheet metal thickness, bend radius and material quality. These are the factors that can be used to establish the layout of the workpiece to be bent.
The tools
Many types of press brake tools are available, such as radial, gooseneck and bending/flattening tools, for which the load limit becomes a decisive factor. There are two limits to consider: the limit that the tool itself can withstand, and the load limit at the centre line of the press brake. When it comes to tools, take great care to choose the correct tool and consider the load that the tool can withstand. Work is often carried out at the tool load limit, which risks damaging the punch and die. To avoid damaging tools or even worse the press brake, always observe the load limits.
Cleaning
Dirt particles can enter the hydraulic circuit if it's not sealed properly, so make sure that the tank cover and breather seals are in good condition. The breathers are fitted on the tank cover, and allow air to flow into the tank to avoid creating a vacuum inside when oil is pumped into the cylinders.
Dirt in the oil can result in malfunctions and faults in the pump and valves. Most hydraulic circuit problems are related to contaminated oil, which can cause the valves to stick in the “on or off” position. This means that tool cleaning is very important: dust, oil, debris, chips and other material that builds up over time can scratch the workpiece surfaces.
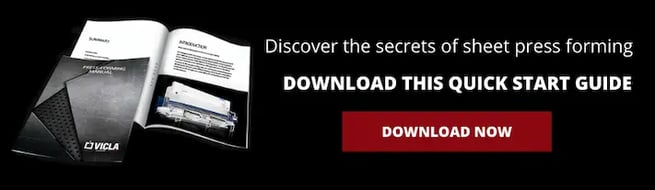