Bending steel and high-strength materials requires perfect precision and parallelism, as even the slightest variation can affect the mechanical and aesthetic characteristics of the finished product.
The widespread use of these materials in various sectors beyond the more established construction, earthmoving, naval, railway, industrial vehicles, and container industries, has presented new challenges for press brake manufacturers. To meet these demands, it has been necessary to refine multiple aspects, from camber control to force management. Vicla, specializing in the design and construction of press brakes, shears, and automated sheet metal bending solutions, has been able to meet these needs by introducing various innovations and technological advancements over the years.
"These solutions," explains Marcello Ballacchino, founder and owner of the company along with Corrado Nucci, "are the result of a decade-long collaboration and are adopted across our entire range of hybrid press brakes, including those in our top-of-the-line .Superior line."
One such installation was recently completed on a 641-ton machine with a 4,600 mm working length – the most powerful ever produced by the company at its plant – commissioned by a major Italian manufacturer of trailers and semi-trailers.
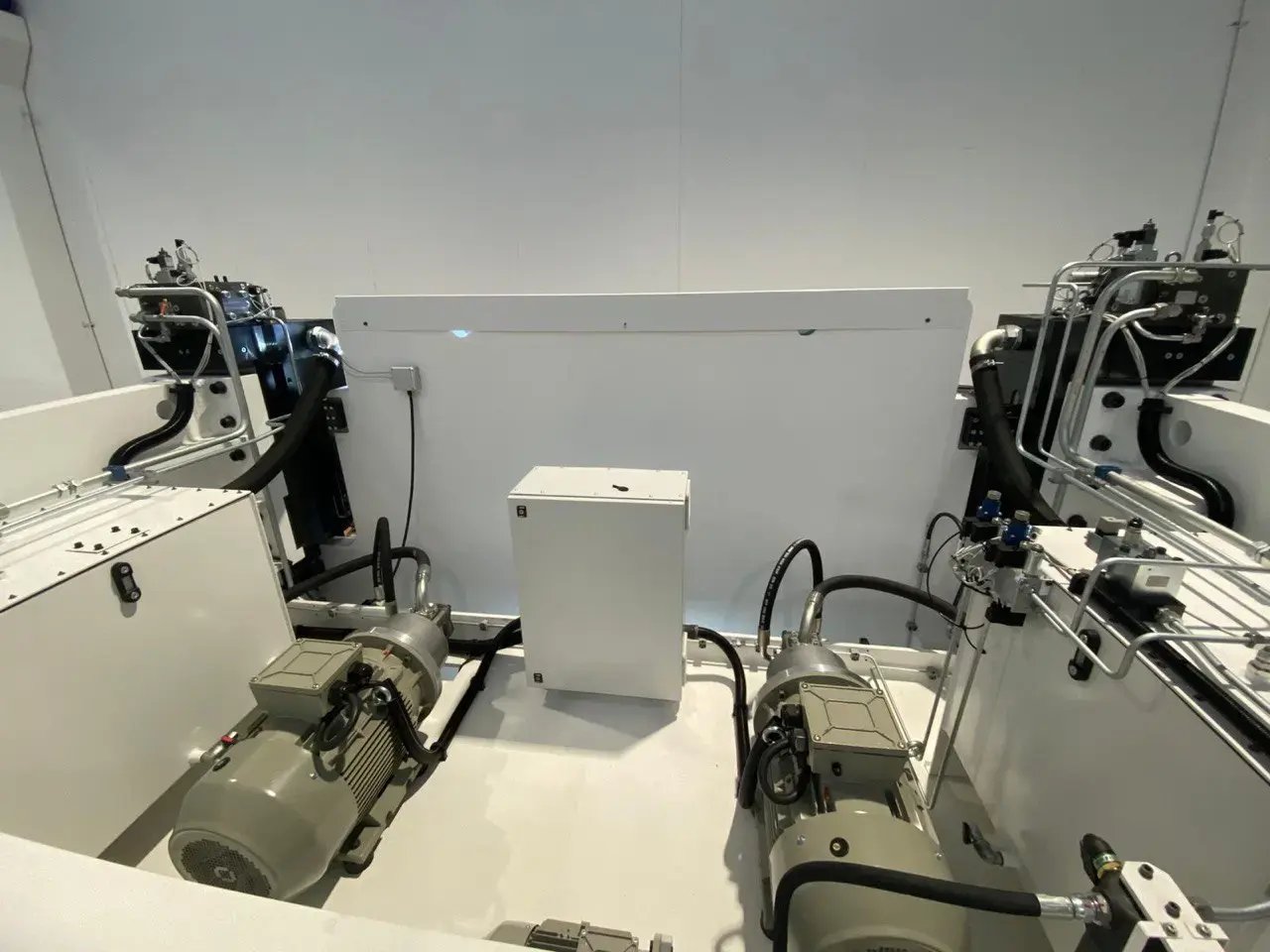
The press brake configuration
The 641-ton .Superior hybrid press brake is a high-quality, high-performance machine that combines advanced hydraulic technology with optimized electronic management.
Compared to conventional hydraulic press brakes, it offers energy efficiency that allows for up to a 55% reduction in electricity consumption, thanks to a hydraulic system designed to ensure low consumption and less oil use.
Adaptive crowning is one of the distinctive technical aspects, guaranteeing precise control of the bend over the entire working surface.
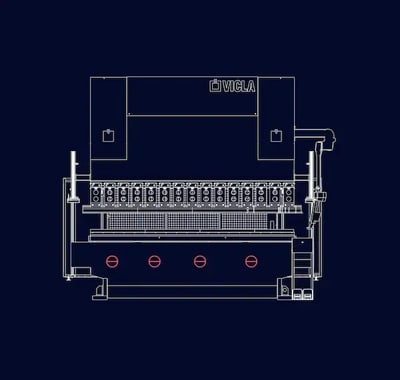
"This technology," says Salvatore Schifano, Vicla's workshop manager, "does not require in-depth technical knowledge. The system automatically adjusts the compensation for a linear bend, even on non-uniform materials, such as perforated/slotted elements mixed with solid material."
At the customer's request, the .Superior press brake was developed with a rear stroke of 1,500 mm, compared to the more standard measurements of 700 or 1,000 mm. With a power of up to 641 tons over a 4,600 mm working length, the .Superior hybrid press brake produced by Vicla for a manufacturer in the trailer and semi-trailer construction sector stands out for its modularity and capacity for future upgrades. The version produced is already very high-performing and complete, with a cylinder stroke of 500 mm, an opening of up to 800 mm, and a rear stroke of up to 1,500 mm.
"The equipment," adds Nucci, "includes high-load tooling, supplied by one of our qualified partners, and a lower clamp with hydraulic locking for faster die changes. It is possible to mount dies with a 60 or 90-degree base, adapting to even larger sizes."
Two sliding, orientable, and height-adjustable front supports, based on the mounted die, faciitate operations, while a real-time angle control system ensures precision.
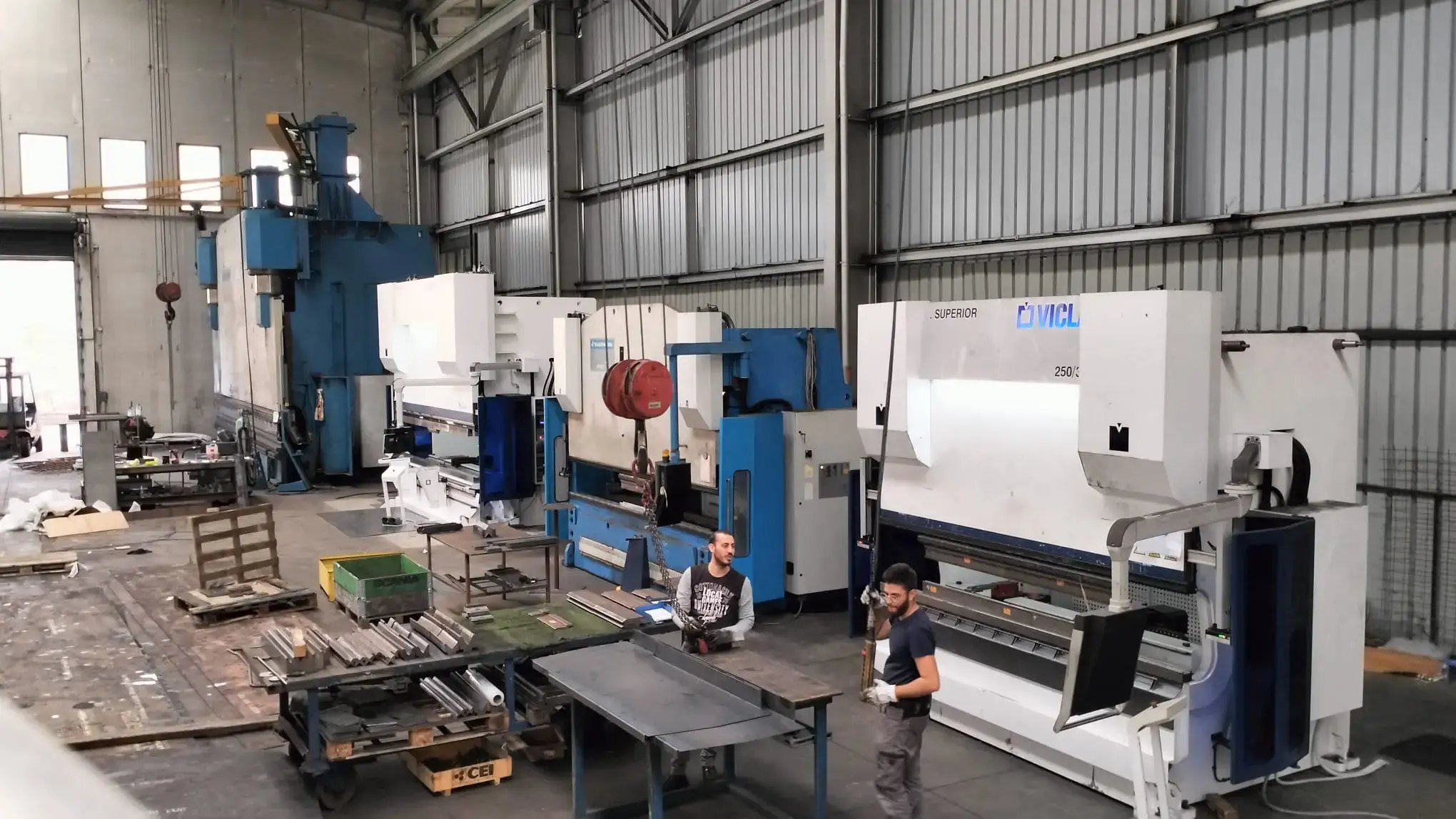