Those who work in sheet metal fabrication know that shaping metal, even on an industrial scale, is a true art.
When discussing sheet metal deformation, it's essential to understand the different bending techniques, as each influences the final product's design and functionality.
A solid grasp of press brake operation, combined with a strong foundation in design principles, can significantly enhance the quality of the finished piece.
Types of Sheet Metal Bending
Sheet metal bending is a cold working process that permanently deforms the material by applying force through a punch. There are several bending techniques, each suited to different desired outcomes.
Three-Point Bending
This category includes air bending, bottoming, and coining.
Air Bending
In air bending, the sheet is suspended in air and the punch presses down on it, creating a bend. This method is versatile and allows for a wide range of bend angles.
Bottoming
Bottoming involves the punch fully contacting the bottom of the die, resulting in a more defined and consistent bend. In contrast with air bending, the principal point here is that the workpiece touches the walls of the die while being bent, forcing sheet metal into precise forms.
Coining
Coining is a high-force process that compresses the material between the punch and die, producing a very sharp bend. Coning is implemented in any case when a manufacturer needs a sheet metal to be stamped.
It causes permanent deformation of the workpiece into the shape required. At the same time, it makes a workpiece to take the form engraved on the surface of the bottom die, if necessary.
Hemming or Flattening
The hemming technique, which requires specific tooling, is used for example to create edges that are safe to handle, or to reinforce thin sheet metal.
It is usually performed in a two-step process:
- pre-bending creating an angle ranging from 35° to 26° (according to the sheet metal thickness) obtained with air bending process
- flattening process where the bend is completely or partially closed (hem).
Tangential Bending
This method uses a tangential punch to create bends where access is limited.
Folding
Metal folding involves a specialized automatic sheet metal folding machine where the sheet metal is clamped securely, and a folding beam moves up or down around a pivot point to create the bends. Unlike bending, which is often limited to single-axis deformation, folding allows for multiple bends in a single operation.
This technique is well-suited for creating complex, three-dimensional shapes with interconnected bends, enhancing design flexibility and efficiency.
Factors Affecting Bend Quality
- Material Properties: as explained in detail in this dedicated article, the type of metal, its thickness, and its hardness all affect the bending process.
- Tooling: the design of the punch and die, as well as their material, play a crucial role in achieving the desired bend. Read this guide and learn which are the most comming tooling in a press brake.
- Machine Setup: proper machine setup, including bed height, backgauge position, and tonnage, ensures accurate and repeatable bends; this is why we create a comprehensive guide which explains every single component of a press brake.
- Bending Technique: the chosen bending technique, whether it's air bending, bottoming, or coining, will impact the final result.
Benefits of Sheet Metal Bending
- Versatility: Sheet metal bending can be used to create a wide variety of shapes and components.
- Precision: Modern press brakes and tooling enable highly accurate and repeatable bends.
- Efficiency: Automation and CNC controls have significantly increased the speed and efficiency of sheet metal bending.
- Cost-Effectiveness: Sheet metal bending is a cost-effective way to produce custom metal parts.
Conclusion
Sheet metal bending is a complex process that requires a deep understanding of materials, tooling, and machine operation. By carefully selecting the appropriate bending technique and equipment, manufacturers can produce high-quality components that meet the demands of various industries.
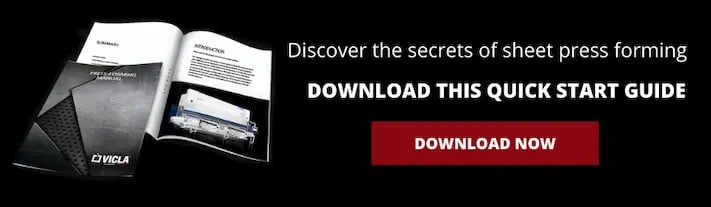