The choice of the right material is fundamental for any sheet metal fabrication project. Understanding the composition and characteristics of these materials, how they interact with the press brake, and the variables of the sheet metal itself, is essential for accurate development calculations. Different materials offer unique characteristics that can significantly influence the strength, durability, workability, and aesthetic appearance of the final product.
Steel
Throughout history, steel has always been employed in a highly versatile manner. This material has been indispensable for technological innovation worldwide. In fact, without its availability and low cost, the Industrial Revolution would not have been possible. Over time, steel production techniques have been perfected. When discussing steel, it's useful to distinguish between two main families:
-
Unalloyed steels: Composed of iron and carbon alloys.
-
Alloyed steels: Alloys containing elements in addition to iron and carbon. Beyond the presence of elements, there are different types of steel based on the percentage of carbon present.
In general, the higher the carbon content, the greater the hardness. When referring to mild or hard steels, we're talking about the carbon concentration. Generally, steel can be classified into these categories:
-
Extra mild: 0.5-0.25% carbon
-
Mild: 0.15 – 0.25% carbon
-
Semi-mild: 0.25 – 0.40% carbon
-
Semi-hard: 0.40 – 0.60% carbon
-
Hard: 0.60% - 0.70% carbon
-
Very hard: 0.70% - 0.80% carbon
-
Extra hard: 0.80 – 0.85% carbon
Alloyed Steels
We've mentioned that alloyed steels are metals that mix other elements besides iron and carbon. One of the most famous is undoubtedly stainless steel.
Stainless Steel
Stainless steel is composed of a high percentage of chromium, which makes the material highly resistant to corrosion and temperature; chromium also provides great malleability, making stainless steel a material used in countless applications.
In press braking, various types of stainless steel are used, each with specific characteristics that make them suitable for particular applications. The most commonly used types of stainless steel are:
300 Series Stainless Steel
-
Stainless Steel 304: This is the most common and versatile type of stainless steel and is also known as 18/10 stainless steel due to the percentages of chromium and nickel present in the alloy. It's known for its excellent corrosion resistance and formability. This material is often used in applications requiring high corrosion resistance, such as commercial kitchens, appliances, and food processing equipment.
-
Stainless Steel 316: In addition to nickel and chromium, it also contains molybdenum, which further improves corrosion resistance, particularly against saline and chemical environments. It's widely used in marine, chemical, pharmaceutical, and medical applications where the environment is particularly aggressive.
400 Series Stainless Steel
-
Stainless Steel 430: This is a type of ferritic steel with good corrosion resistance and good mechanical properties. It's often used for internal applications such as appliance panels and architectural cladding. However, compared to the 300 series, it has lower corrosion resistance and lower malleability.
-
Stainless Steel 410: It offers a good balance between corrosion resistance and hardness. It's used for applications requiring high wear resistance and moderate corrosion resistance, such as cutting tools, blades, and industrial equipment.
Cor-Ten Steel
Cor-Ten steel, also known as weathering steel, is a special alloy with a brownish-red color. The name COR-TEN comes from the combination of "corrosion resistance" and "tensile strength," highlighting its main characteristics of corrosion resistance and tensile strength.
The primary property of Cor-Ten steel is its rare and unique ability to self-protect naturally from corrosion, an oxidative reaction that responds to environmental stresses and leads to the development of a surface oxide patina that, if scratched or removed, constantly regenerates over time.
Aluminum
Aluminum is another highly popular material in sheet metal fabrication due to its lightweight nature, corrosion resistance, and ease of processing. It finds applications across a broad spectrum, from aerospace to automotive and even household appliances. Aluminum can be anodized to further enhance its corrosion resistance and aesthetic appeal.
Copper
Copper is renowned for its exceptional electrical and thermal conductivity, making it perfect for electrical and heating applications. It also exhibits good corrosion resistance and can develop a protective patina, lending it a unique and appealing appearance. However, copper is relatively expensive and often used in specialized applications.
Brass
Brass, an alloy of copper and zinc, is valued for its ease of processing, corrosion resistance, and golden appearance. It's widely used in decorative components, musical instruments, and plumbing fixtures. Its malleability allows for the creation of intricate and precise details, making it ideal for precision work.
Titanium
Titanium is a highly durable and lightweight material known for its exceptional corrosion resistance and ability to maintain its structural integrity even at high temperatures. It's employed in industries demanding superior performance, such as aerospace, medical, and military. The downside is that titanium is expensive and requires specialized processing techniques.
The choice of material for sheet metal fabrication depends on a variety of factors, including the desired mechanical properties, corrosion resistance, cost, and the specific application. Each material offers unique advantages and can significantly influence the production process and the performance of the final product. Understanding the characteristics and interactions of these materials is essential for successful sheet metal fabrication projects.
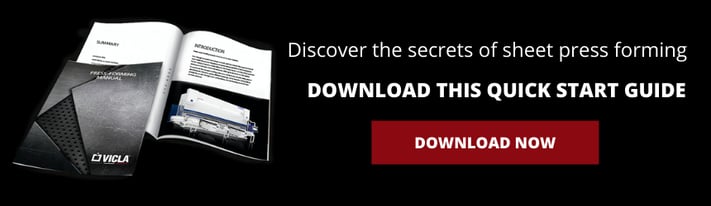